Vehicle teardown expert Sandy Munro has decades of automotive engineering experience on his resume. He just recently started tearing down a Tesla Model S Plaid. In about a half-hour-long video analysis he unveiled the secrets of the Plaid battery pack (watch below).
The first time a Tesla battery pack teardown and analysis was performed by the late and great Jack Rickard back in 2018. When Jack opened up a Model 3 battery pack at the time, he was amazed at the engineering effort Tesla had put into it.
Fast-forward about 3 years, the Model S Plaid still impresses the best of engineers the world has today, “It’s an engineering masterpiece,” says Sandy Munro.
“That was a tough one. New Model Y structural pack is next-level though,” Tesla CEO Elon Musk tweeted while commenting on Munro’s review of the Plaid battery pack.
Tesla Model Y electric SUVs produced at Giga Texas and Giga Berlin will be the first Tesla cars with structural battery packs. Last year during the Giga Fest celebrations in Berlin, Tesla showed the Model Y structural battery pack to the public visitors. Model Y seats will be directly mounted on the battery pack and it will be the floor of the vehicle itself.
Let’s go over some major features and revelations Sandy Munro talked about in his video on the Model S Plaid battery pack teardown.
Jump to read the desired topic:
- Mica Shield
- Concentric Welding
- Impact Mitigation and Module Castings
- Pressure Valves
- Wiring, Modules, Cells, and the Penthouse
- Efficiency
- Miscellaneous Findings
Mica Shield
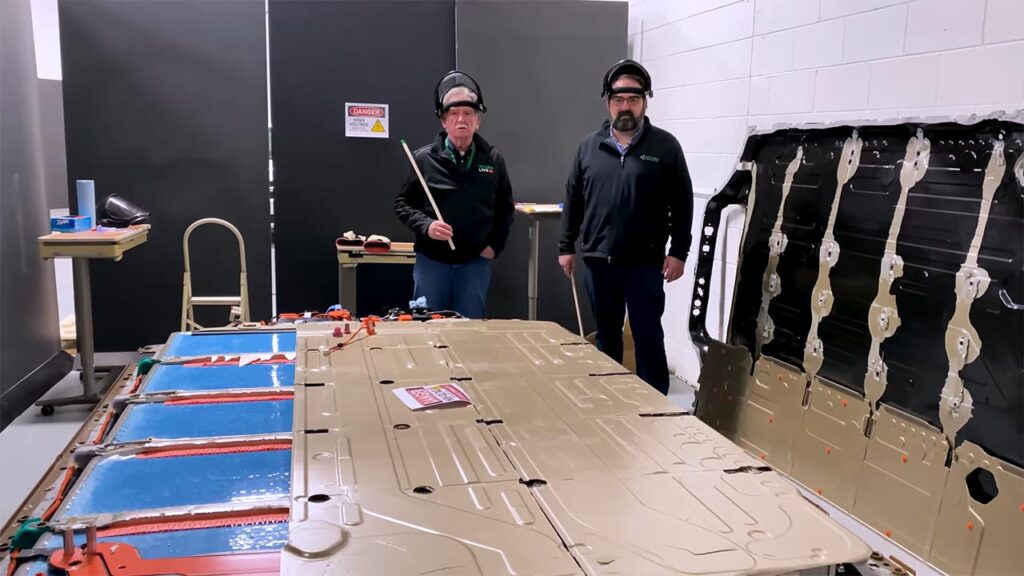
As we can see in Fig 1 above, when the main metal cover of the Plaid battery pack is removed (far right), there is another shield over the battery modules covering roughly about 70% of the area. According to Sandy Munro, this is a mica shield that is normally used in liquid-level gauges to protect the glass surface from corrosion caused by hot alkaline or acidic solutions (source: BoilerSupplies.com).
The co-host of the show Ben Lindamood explained why Tesla must have put this extra shield in place. Ben thinks that this shield is in place because there are strict fire mitigation requirements imposed in China.
This mica shield acts as a fire retardant, Ben thinks. However, Sandy Munro thinks Tesla should have used fire-retardant plastics that don’t require mining.
This mica shield is a new addition to the Plaid battery pack as it was not present in the Model 3 or Model Y battery pack when Sandy tore it open back in 2020.
Concentric Welding
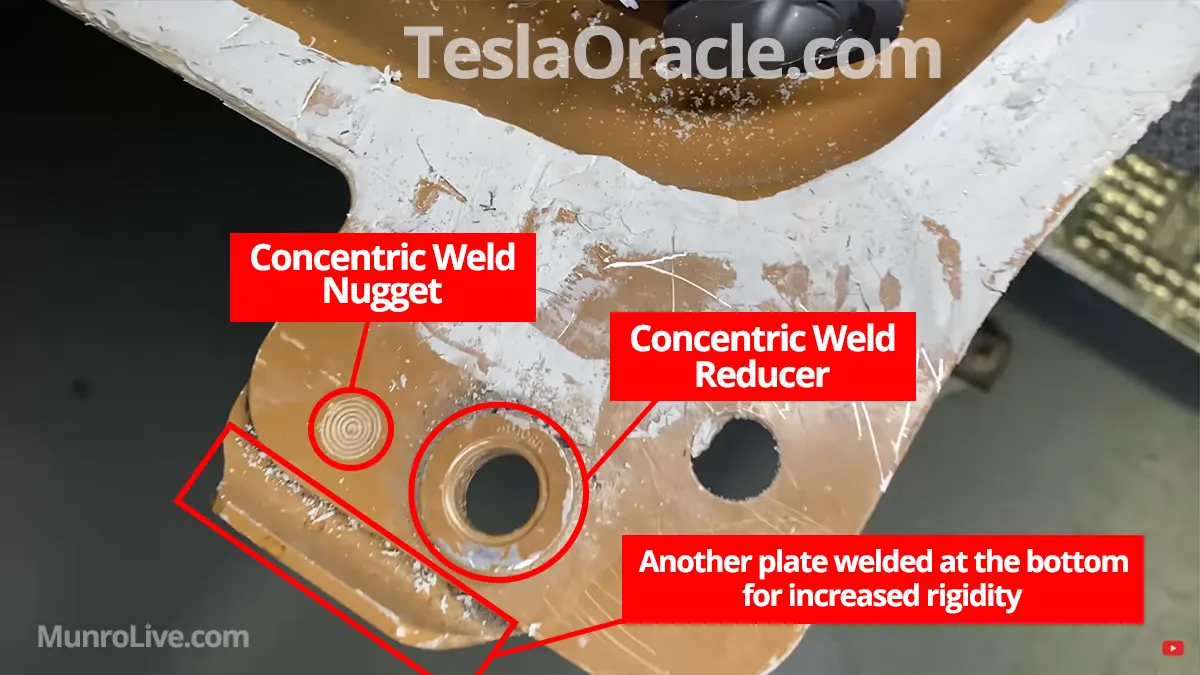
To weld the bottom plates of the battery pack, Tesla has used a welding technique known as “concentric welding”. According to Sandy Munro, this technique was invented by General Motors in 2012 and GM also holds a patent for this technique.
Concentric welding increases the life of the weld tips by about 3 times so there is less need for changing the weld tips while welding aluminum to aluminum plates. It also increases the life of the weld machines, Ben explained.
As we can see in the image above, Tesla has welded another plate under the battery pack for increased rigidity. Concentric weld nuggets are also bigger and substantially stronger compared to the normal weld nuggets, Sandy further described.
Impact Mitigation and Module Castings
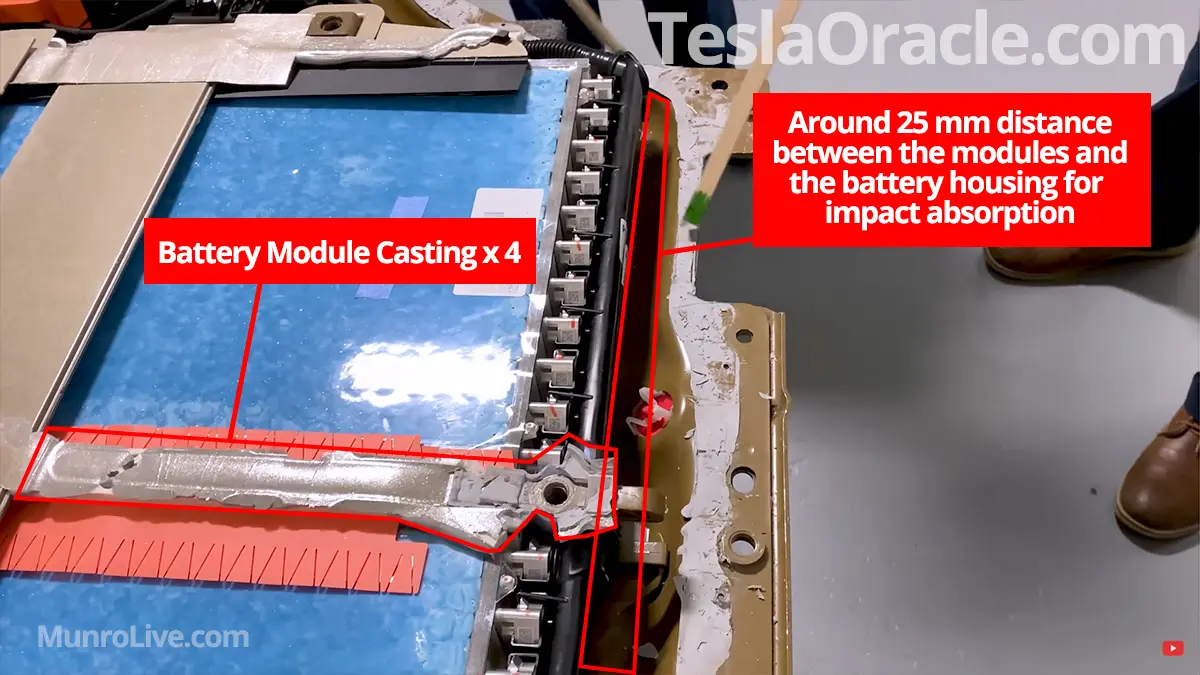
Sandy Munro points out an important feature Tesla has kept in the Plaid battery pack, the space we see in Fig 3 above. According to Ben’s engineering knowledge, this space is kept to absorb any impact and let the metal housing deform first before the impact hits the module. Some intelligent engineering by Tesla here.
We can also see one of the 4 castings that Tesla has put in between the 5 modules of the Plaid battery pack. The side castings are different than the middle ones. Tesla has become a fan of large castings as well as small to reduce the number of parts and welds and this methodology can be seen in the new battery packs as well.
Pressure Valves
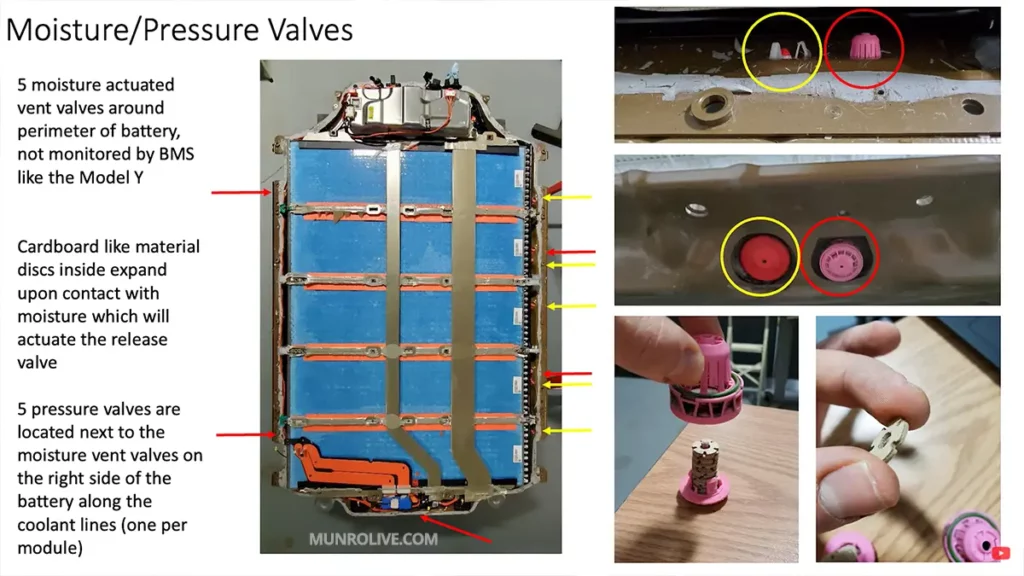
One interesting new feature that Sandy Munro and his engineering team have explored in the Tesla Model S Plaid battery pack is the moisture actuated pressure-release valves. There is a total of 5 vent valves installed, one for each battery module as we can see in Fig 4 above.
Wiring, Modules, Cells, and the Penthouse
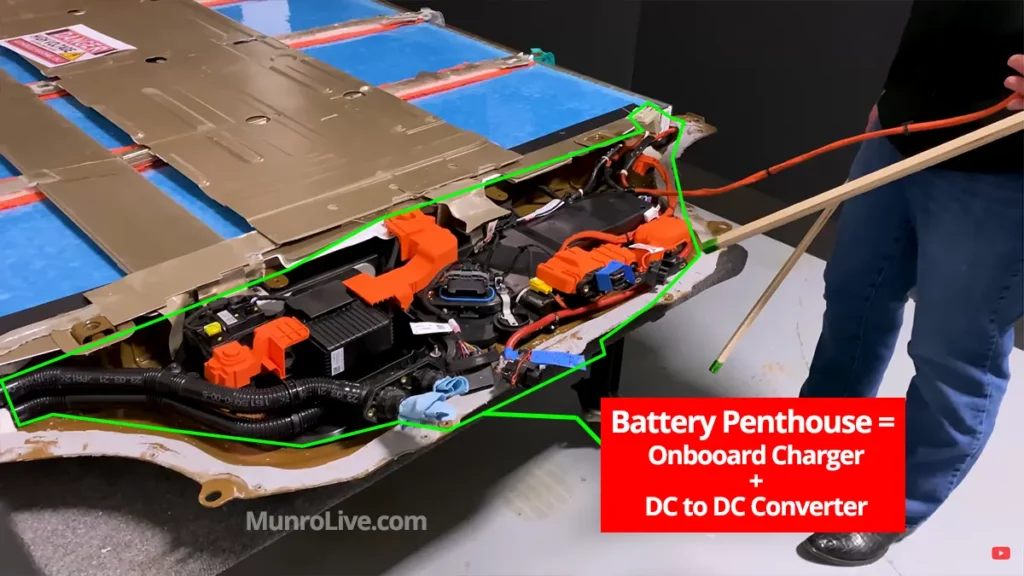
The Model S Plaid battery pack has the charging input on one end and the onboard charger and the DC to DC converter system on the other. This setup gives a slimmer battery penthouse (Fig 5 above) compared to the previous Model S and also the current versions in Model 3 and Model Y.
I labeled a Tesla Model 3 battery pack penthouse back in 2018 as described by late Jack Rickard (see Fig 6 below). The charging input port and the 12-volt output connector being on the same platform saved quite a bit of wiring in this setup.
To connect the charging input system to the penthouse in a Plaid battery pack, Tesla had to use a lengthy wire (see Munro’s video below at 10:35).
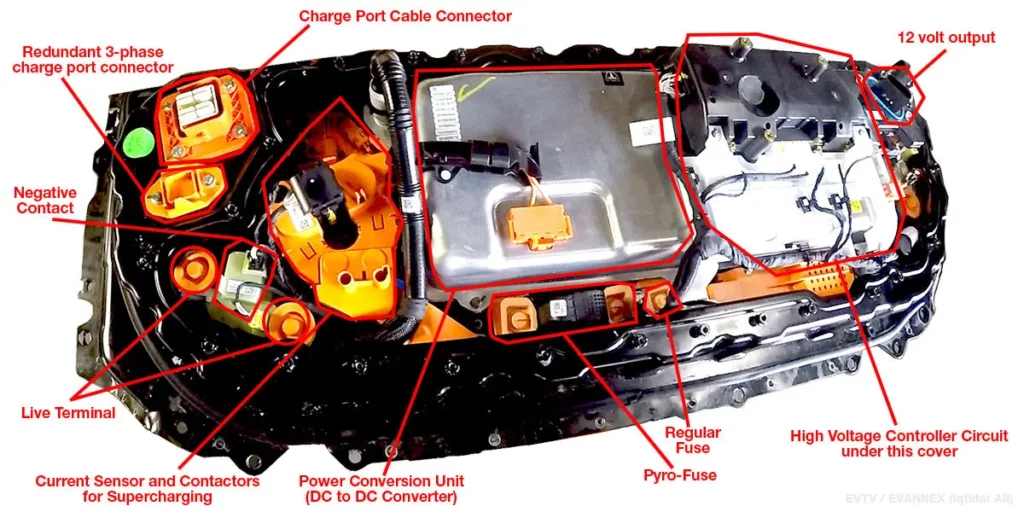
Last year, a YouTube channel named Ingineerix also tore down a Model S Plaid battery pack and found out the following details of the modules and cells in it.
The Tesla Plaid pack uses 7,920 18650 cells arranged in 5 modules that have a 72P22S arrangement each (total of 72P110S). Same BMS system as Model 3/Y. It is capable of sustained 2300A output at a max voltage of 462V (That’s over 1 megawatt).
Each module is 15 3/8″ (390mm) long X 55 1/4″ (1404mm) wide X 3″ (76mm) high. If you include the coolant manifolds and lines, the width is 57 3/8″ (1458mm).
Comparing the Plaid on-board charger and DC to DC converter with a 2020 Model Y setup, Munro and his team found out that Tesla was able to reduce around 1.2 kilograms (2.64 lbs) of weight from the entire circuit.
Efficiency
Munro & Associates have found out that although the Plaid battery uses the old 18650 cell form factor, Tesla was able to increase the efficiency of the pack significantly.
In the older Model S, it used to be 157 Watt-hours (Wh) per kilogram of the pack weight, with the Plaid, it has now jumped to 181.5 Wh / kilogram. So, with about the same 100 kWh battery, Tesla is able to extract more range, perhaps the cell chemistry has a big role at play here.
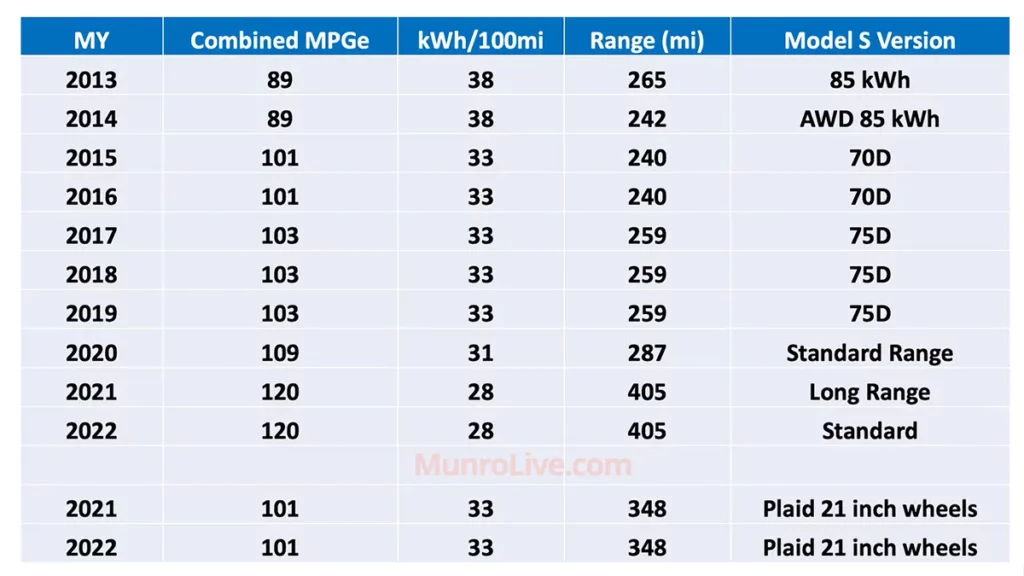
Miscellaneous Findings
Sandy Munro finds it fascinating that Tesla has been able to design two fairly different cars (Model Y SUV and the Model S Plaid performance sedan) using a good number of common components like the onboard charger and other circuits.
Not only did Tesla re-use the old components from the lineup here, the automaker also improved upon the system by modifying them and even removing the ones not needed anymore.
Munro recalls the strategy of traditional automakers was based on the standards they had made, in-the-end these standards resulted in added cost and weight of components.
It’s impossible to ignore how much more effective and efficient over anything else we have seen.
Sandy Munro talking about Plaid battery electronics.
Stay tuned as we will be covering more areas of the Tesla Model S Plaid teardown.
Stay tuned for constant Tesla updates, follow us on:
Google News | Flipboard | RSS (Feedly).
Related:
- Elon Musk unveils the Tesla Robotaxi (Cybercab) — shares the price and launch timeline
- The new Tesla Referral Program is less complicated yet more rewarding
- Tesla Model Y RWD owners can unlock 50 miles of extra range for $1,600 via an OTA update
- Tesla celebrates July 4th by offering free Supercharging and $1,000 discount for members of the U.S. military